The processing of industrial hose assembly includes hose cutting, stripping, hose and joint assembly, crimping and cleaning.
Cutting
Hose materials should be within the expiration warranty period. There should be no quality defects such as breakage, blistering, bumps, etc. Cut with a blade or a grinding wheel. The verticality of the cut section to the hose axis should not exceed 6°. In addition, use a nylon brush to clean the cut part and inner surface of the hose to remove the residual rubber at both ends. And use compressed air to blow away the dust on the inner surface of the hose.
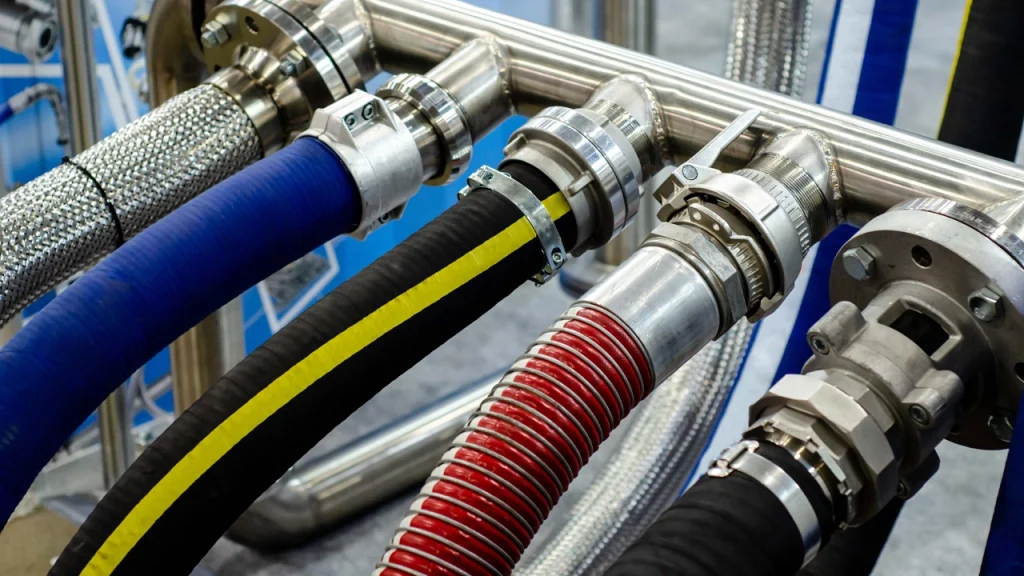
Stripping
Strip the hose that needs to be stripped. If the inner and outer rubber need to be stripped, first strip the inner rubber and then the outer rubber. The thickness of the residual rubber at the stripping point is ≤0.8 mm, and the steel wire cannot be damaged.
Assembly
The non-stripping joint needs to be marked on the hose according to the sleeve length before assembly. A small amount of lubricating oil can be used for the over-tight joint and assembled with a pipe loader. The stripped part of the stripped hose cannot be exposed. Confirm whether the non-peeling hose is assembled in place according to the drawn line position.
Crimping
Use special crimping equipment, select the crimping mold, set the crimping size of the equipment, and crimp. After crimping, different specifications of hoses must be tested for the first time. The minimum crimping size + 0.05 mm ≤ the actual size of the first inspection ≤ the maximum crimping size – 0.05 mm. Otherwise, the crimping size of the equipment needs to be reset.