Steel wire spiral hoses are common in various industries, but using them requires careful attention. This prevents issues like pipe rupture or oil leakage. So, what should you focus on during use?
4 Key Factors for Using Steel Wire Spiral Hoses
First, avoid making the hydraulic hose’s bending radius too small. Steel wire hoses handle very high internal pressure, which concentrates on bent areas. Over time, this damages the inner rubber tube, leading to leaks. A tight bend also stretches the outer rubber layer, increasing the risk of cracks. Additionally, leave a straight section where the spiral hose assembly connects to the pipe joint—this section should be at least twice the hose’s outer diameter in length.
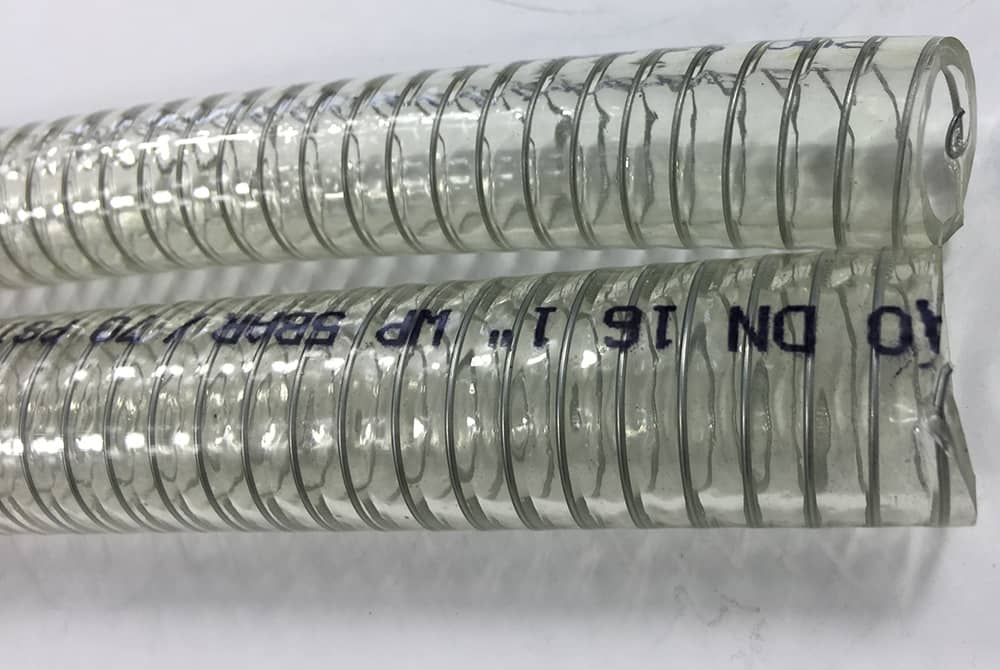
Second, hoses shrink and deform when pressure is applied. Typically, they shrink by 3–4% of their total length. For this reason, install steel wire hose assemblies slightly longer than needed. This prevents them from staying in a stretched, tense state during use.
Third, ensure the wire spiral hose assembly doesn’t twist or deform during installation. Align the joint axis of the wire-wound hose with the plane of motion as much as possible. This reduces the risk of damage to the spiral wire hose.
Last, keep flexible spiral hoses away from sharp machine corners. Sharp edges can scrape or cut the outer rubber layer, damaging the pipe.
By following these tips, you can extend the life of steel wire spiral hoses and avoid costly leaks or failures.